Uptime is the real currency of modern manufacturing. When blast equipment stalls or compliance paperwork is overdue, every minute eats into margin. SurfacePrep UK has built a service ecosystem that removes that drag on performance, from operator training to licensed abrasive recycling.
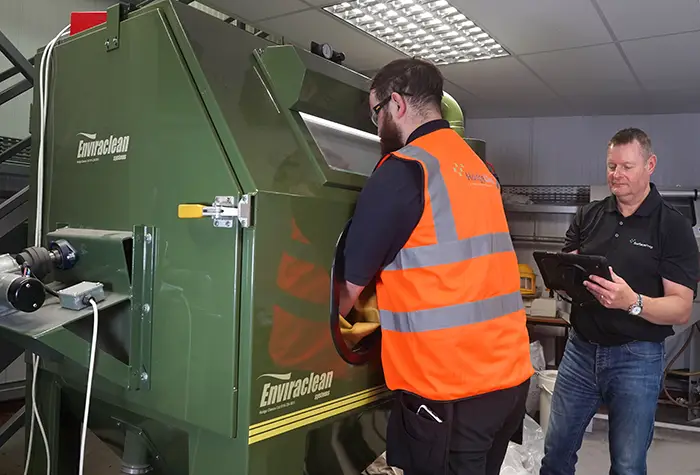
Operator Training: faster starts, fewer failures
Classroom theory is useful, but mechanical sympathy is learned with a blast nozzle in hand. SurfacePrep courses cover PPE, health and safety, maintenance and live fault-finding, then issue recognised certificates that satisfy insurers and auditors. The impact is immediate: operators hit specification first time and rework falls away.
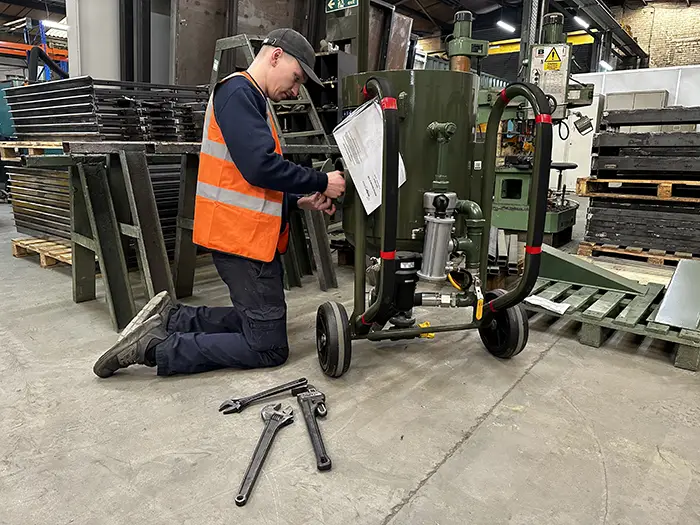
Reactive and Preventive Servicing: 60 years of field data on tap
Abrasive blasting is hard on valves, seals and pressure vessels. SurfacePrep engineers draw on six decades of equipment-building experience to spot wear early and fix it first time. Three Total Care packages, Gold, Silver and Bronze, let plant managers choose the response time, visit frequency and payment terms that match their production risk.
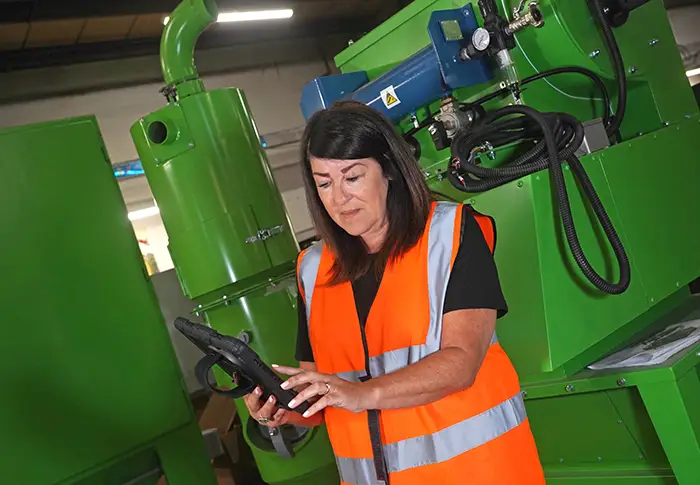
Testing and Compliance: paperwork that passes first time
P601 LEV tests, pressure-vessel examinations, breathing-air audits, all mandatory, all time-consuming. SurfacePrep’s compliance team arrives with calibrated kit and issues reports that satisfy insurers and the HSE in one visit. That prevents repeat site visits and unplanned production stops.
Recycling and Waste Disposal: cut abrasive spend by up to 30 percent
As licensed waste brokers and carriers, SurfacePrep collects spent abrasives, keeps them out of landfill and repurposes them for other industries, reducing disposal fees and shrinking ESG footprints.
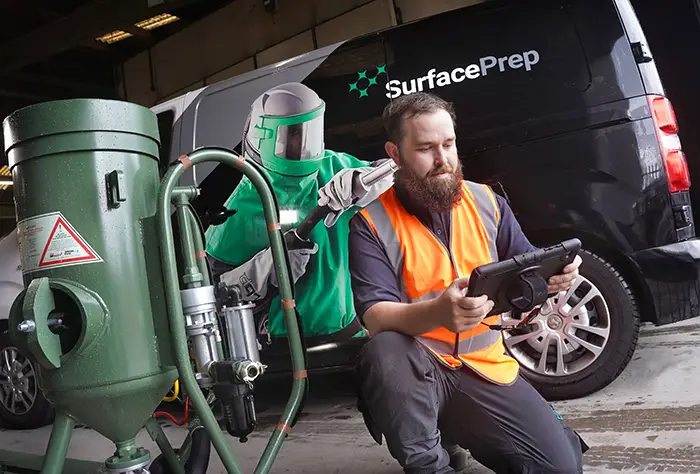
Equipment Hire: capacity on demand
Urgent shutdown, one-off contract or CAPEX freeze, the hire fleet covers portable blast pots, closed-circuit units, Doosan compressors and wet-paint pumps. All kits ship with air lines, PPE and on-site training, with nationwide delivery and collection.
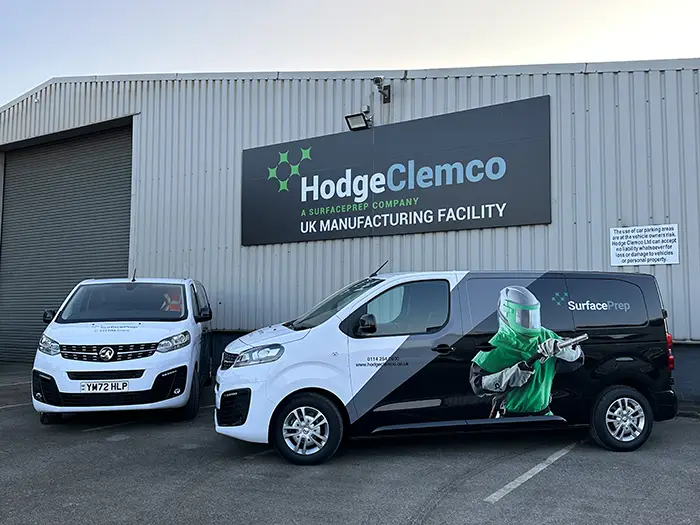
Not every project justifies brand-new hardware. SurfacePrep strips, tests and guarantees used Smart Cabs, suction cabinets and e-Xtreme pumps; stock levels are posted online and change weekly.
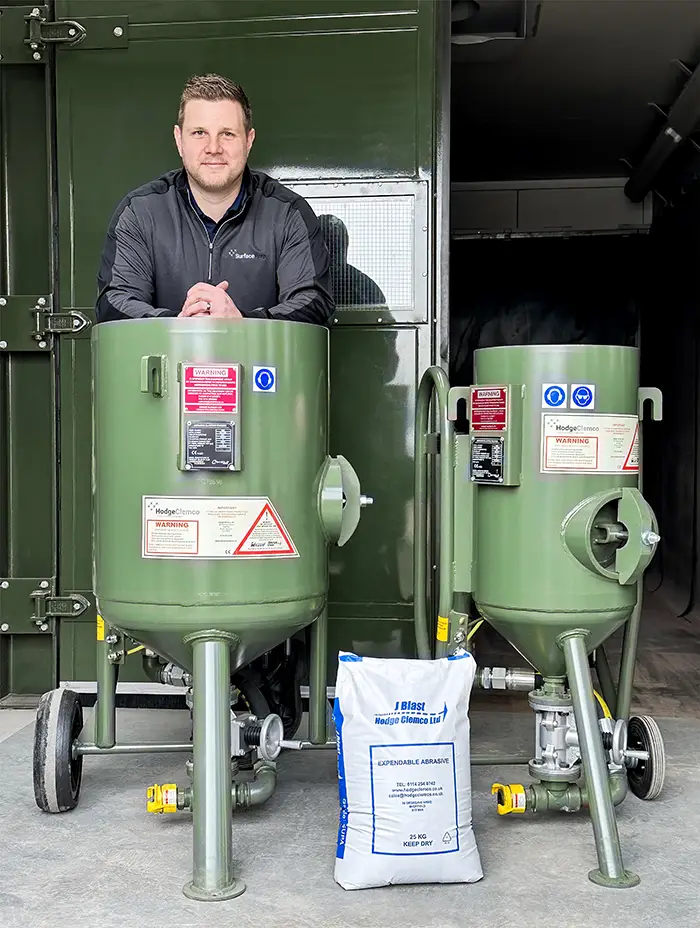
Need a Thompson valve today or help specifying a bespoke blast room? One technical desk covers consumables, machinery and application engineering. With the UK’s largest inventory of blasting spares, downtime is measured in hours, not days.
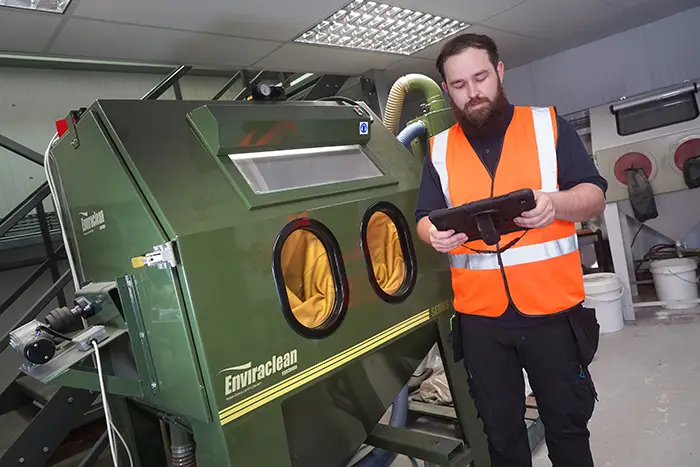
- Operator Training: removes operator error, delivers higher right-first-time rates
- Total Care Servicing: prevents breakdowns, makes OPEX predictable
- Compliance Testing: avoids HSE or insurer shutdowns, keeps production live
- Abrasive Recycling: lowers disposal costs, improves sustainability metrics
- Equipment Hire: fills temporary capacity gaps without capital spend
- Refurbished Kit: cuts lead-time and depreciation on replacement assets
- Spares and Advice: slashes mean-time-to-repair with parts on the shelf
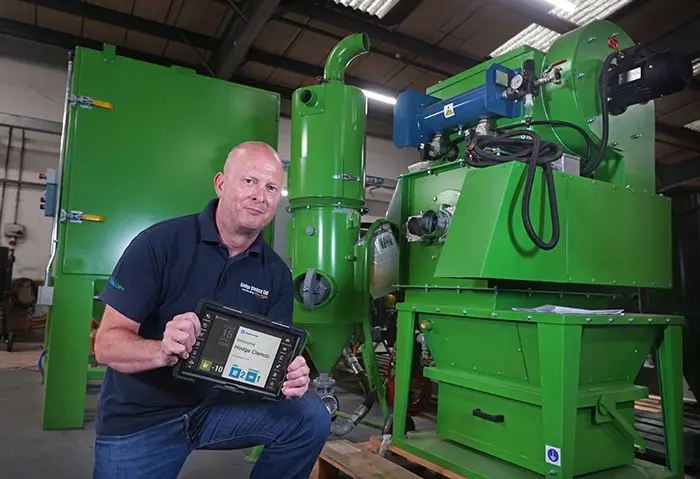
SurfacePrep’s service architecture mirrors the equipment lifecycle: specify, install, certify, maintain, upgrade and, finally, recycle. One purchase order, one phone number, and no gaps between suppliers. For businesses that value uptime, that simplicity converts directly into profit.
Call 0114 254 0600 or email